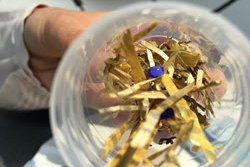
© ISOBIO
The ISOBIO project aims to develop construction materials with 50 % lower embodied energy and carbon, and 20 % more efficient thermal insulation compared with traditional oil-based insulation panels. The project also seeks to demonstrate a reduction of at least 15 % in total costs and 5 % in total energy spent over the lifetime of a building.
‘We hope to develop materials that are competitive in every sense,’ says Dr. Alan Taylor, project coordinator and Technology Fellow at TWI in the UK. ‘We want to solve the “trilemma” of guaranteeing the security of supply of materials, producing materials that have a genuine competitive edge, and reducing emissions.’
Back to the future for building materials
ISOBIO started by identifying promising organic materials that could be used as insulation. Many of these are classified as waste or byproducts of processes like food production. Finely chopped bio-materials such as hemp and straw are treated with hygrothermal resins and nano-particle gels that make them robust, breathable, moisture resistant, and fire retardant.
The bio-aggregates are typically the result of combining organic and inorganic materials; the organic material may have natural insulating properties, for example, while the inorganic material may make the resulting bio-aggregate more robust. Combing organic materials with inorganic materials is not always easy, however. Hemp, for instance, is being combined with lime mortar but the two materials have a degree of chemical incompatibility which could result in a reduction in the strength of the composite material. To overcome this challenge, ISOBIO’s researchers are using nano-technology to increase the interfacial strength between the two materials, giving the resulting composite material improved mechanical and structural properties.
Not just a better mousetrap: increasing comfort
The new materials not only improve upon the performance of conventional materials, they also offer new features. Hemp shiv, which is the core of the hemp stalk, for example, has a porous structure that provides moisture buffering to maintain humidity at a more constant level.
‘From a physiological perspective, most people like slow changes,’ explains Dr. Taylor. ‘Yet most conventional materials contribute to big fluctuations in temperature and humidity throughout the day, and produce cold and hot zones in a building.’
According to Dr. Taylor, the situation has been exacerbated by new building standards and techniques designed to reduce energy consumption.
‘We’re moving to almost hermetically sealed buildings, but getting rid of gaps and drafts has resulted in harsh environments in which people may feel uncomfortable,’ he says.
Finding the right balance
While the new composite materials may provide more comfort, they need to be at least as robust as conventional materials. To make the hemp-based bio-aggregate water repellent, for example, ISOBIO’s researchers are applying hydrophobic treatments to it. The result is that water vapour can travel in and out of the material but liquid water cannot penetrate it.
‘We’re striving to find the delicate balance between applying the right level of coating on the hemp shiv and preserving some of its inherent properties such as porosity,’ says Dr. Taylor.
Entering the mainstream
To replace conventional construction materials, ISOBIO’s researchers recognise that they need to offer products that are not only technically but also commercially viable.
‘A key question is: how do we adapt the materials to the existing manufacturing processes for conventional materials?’ says Dr. Taylor.
To find the answer, ISOBIO will manufacture materials and conduct tests on a series of industrial-scale demonstration prototypes.
ISOBIO is also making sure that its products can be compared with conventional ones by quantifying the energy efficiency of conventional materials. As part of its life cycle analysis, the project is analysing over 100 existing materials. Despite these efforts, perception and lack of awareness remain major challenges.
‘A purchasing manager may not consider operating cost, ignoring the thermal performance of a building or the embodied energy used to construct it,’ says Dr. Taylor. ‘We need to move away from “this is the cheapest” to consider whole life cost.’ Moreover, builders need to be made more aware of the new materials, he adds.
Finding a market
Despite the challenges, the market for ISOBIO’s composite materials is promising. On the supply side, sourcing local organic materials helps reduce transportation costs, while using waste or byproducts as inputs helps control the cost of the final product. On the demand side, Dr. Taylor believes that demographic trends are leading to a shortage of housing, and especially affordable housing. Increasing the availability of new and affordable housing will require novel construction methods and designs that allow more rapid construction, he asserts.
‘We hope to develop materials that are competitive in every sense,’ says Dr. Alan Taylor, project coordinator and Technology Fellow at TWI in the UK. ‘We want to solve the “trilemma” of guaranteeing the security of supply of materials, producing materials that have a genuine competitive edge, and reducing emissions.’
Back to the future for building materials
ISOBIO started by identifying promising organic materials that could be used as insulation. Many of these are classified as waste or byproducts of processes like food production. Finely chopped bio-materials such as hemp and straw are treated with hygrothermal resins and nano-particle gels that make them robust, breathable, moisture resistant, and fire retardant.
The bio-aggregates are typically the result of combining organic and inorganic materials; the organic material may have natural insulating properties, for example, while the inorganic material may make the resulting bio-aggregate more robust. Combing organic materials with inorganic materials is not always easy, however. Hemp, for instance, is being combined with lime mortar but the two materials have a degree of chemical incompatibility which could result in a reduction in the strength of the composite material. To overcome this challenge, ISOBIO’s researchers are using nano-technology to increase the interfacial strength between the two materials, giving the resulting composite material improved mechanical and structural properties.
Not just a better mousetrap: increasing comfort
The new materials not only improve upon the performance of conventional materials, they also offer new features. Hemp shiv, which is the core of the hemp stalk, for example, has a porous structure that provides moisture buffering to maintain humidity at a more constant level.
‘From a physiological perspective, most people like slow changes,’ explains Dr. Taylor. ‘Yet most conventional materials contribute to big fluctuations in temperature and humidity throughout the day, and produce cold and hot zones in a building.’
According to Dr. Taylor, the situation has been exacerbated by new building standards and techniques designed to reduce energy consumption.
‘We’re moving to almost hermetically sealed buildings, but getting rid of gaps and drafts has resulted in harsh environments in which people may feel uncomfortable,’ he says.
Finding the right balance
While the new composite materials may provide more comfort, they need to be at least as robust as conventional materials. To make the hemp-based bio-aggregate water repellent, for example, ISOBIO’s researchers are applying hydrophobic treatments to it. The result is that water vapour can travel in and out of the material but liquid water cannot penetrate it.
‘We’re striving to find the delicate balance between applying the right level of coating on the hemp shiv and preserving some of its inherent properties such as porosity,’ says Dr. Taylor.
Entering the mainstream
To replace conventional construction materials, ISOBIO’s researchers recognise that they need to offer products that are not only technically but also commercially viable.
‘A key question is: how do we adapt the materials to the existing manufacturing processes for conventional materials?’ says Dr. Taylor.
To find the answer, ISOBIO will manufacture materials and conduct tests on a series of industrial-scale demonstration prototypes.
ISOBIO is also making sure that its products can be compared with conventional ones by quantifying the energy efficiency of conventional materials. As part of its life cycle analysis, the project is analysing over 100 existing materials. Despite these efforts, perception and lack of awareness remain major challenges.
‘A purchasing manager may not consider operating cost, ignoring the thermal performance of a building or the embodied energy used to construct it,’ says Dr. Taylor. ‘We need to move away from “this is the cheapest” to consider whole life cost.’ Moreover, builders need to be made more aware of the new materials, he adds.
Finding a market
Despite the challenges, the market for ISOBIO’s composite materials is promising. On the supply side, sourcing local organic materials helps reduce transportation costs, while using waste or byproducts as inputs helps control the cost of the final product. On the demand side, Dr. Taylor believes that demographic trends are leading to a shortage of housing, and especially affordable housing. Increasing the availability of new and affordable housing will require novel construction methods and designs that allow more rapid construction, he asserts.
No comments:
Post a Comment