Fibre from the industrial hemp plant is one of nature’s wonders – it’s used in everything from stuffing furnishings to high quality textiles.
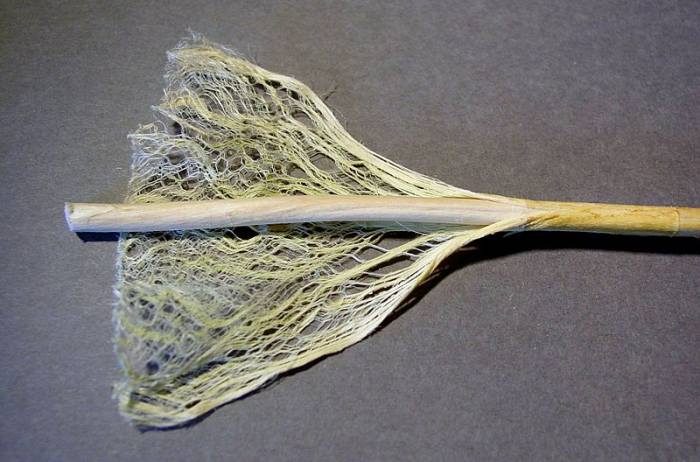
The image above shows a hemp stem. The outer material contains the prized bast fibers and the inner is the hurd, which is made up of short fibers.
There are three main stages of producing fiber from industrial hemp – harvesting, retting and separation.
Harvesting
The quality of hemp fibre depends greatly on whether the crop was grown primarily for textiles, or is dual-purpose. Dual purpose crops produce fiber and seed; with the seed being used for food, biofuels and other applications.
A crop grown specifically for fibre will generally produce a higher quality product than a dual-use crop.
The time at which industrial hemp is harvested is also crucial in the quality of the fiber produced. Hemp grown specifically for this purpose is usually harvested 70-90 days after seeding; early in the flowering stage and well before seed is produced.
Dual purpose hemp crops are harvested later and the fiber isn’t usually used for textiles; but instead for pulp, paper and non-woven products due to the higher lignin content.
When harvesting, the plants are cut at 2 to 3 cm above the soil line and then allowed to dry for a few days.
Retting
Retting is a process involving the use of moisture and microbes to break down the chemical bonds (pectin) holding the hemp stem together, enabling easier separation of the bast from the woody core (the hurd or shiv).
Retting can be carried out a number of ways:
- field retting, where the hemp is left to decompose to a degree naturally through the action of dew, molds and bacteria. This can take anywhere from 4 – 6 weeks depending on the weather and must be closely monitored.
- water retting, through full immersion
- direct use of enzymes
Once the retting process is complete, the stalks are dried to a moisture content of less than 15% and bailed.
Fibre Separation
In a process called “breaking”, stalks are passed between fluted rollers to crush and break the hurd into small pieces, separating some of the fibre in the process. Once a very involved and labor intensive process, separation of the bast from the hurd has been somewhat simplified through a machine called a decorticator. The following video demonstrates a portable decorticator used with another type of plant (jute or kenaf).
Decorticators enable the leaves to be left on the stalks during the breaking, although this makes for a messier process requiring more sorting after completion.
A further process called “scutching” beats and scrapes the fiber bundles, separating more short fiber and the remaining hurd material from the long fiber.
Fiber Types
The short fibers produced during the separation process are known as tow and the long fibres are called line fibre.
Line fibre can be incredibly long – depending on the height of the plant, a single strand may be up to 5 metres in length.
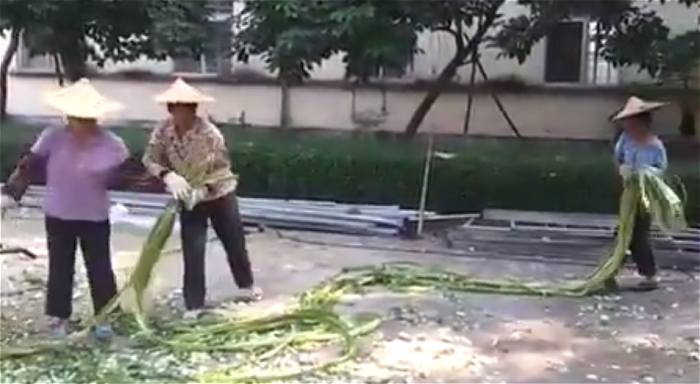
Once separated, the line fibre is cleaned and carded to size, cut and bailed; ready to be further processed and spun. The tow fibre is just compressed and bailed.
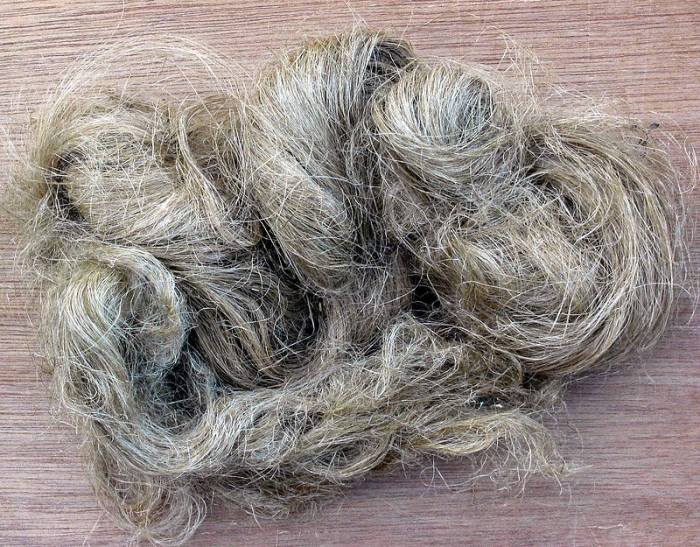
Hemp tow is used for stuffing or coarse yarn spinning and line fibre for higher-end applications such as clothing fabrics, furnishing and floor coverings. Fabrics made from line fibre can have a texture similar to linen; very different to the feel of wearing something akin to a hessian sack that some people may have experienced with hemp clothing
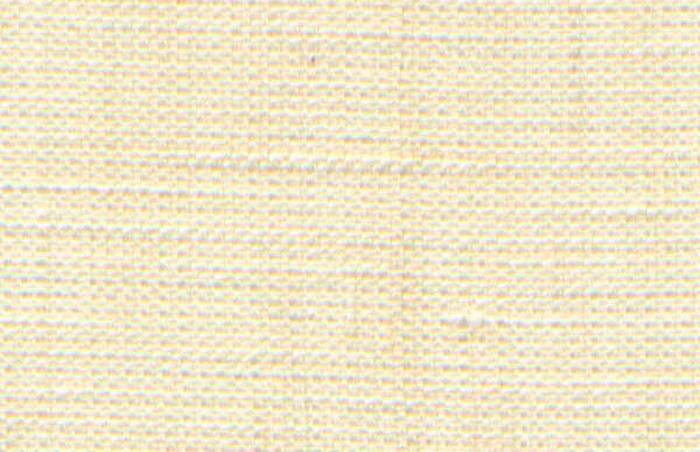
Hemp Fiber Yield
According to a USDA document, 3.5% of the weight of “green” (unprocessed) industrial hemp can be converted dry line fibre and 1% of it to dry tow. This doesn’t mean the rest is waste as just about every part of an industrial hemp plant has value and purpose.
Some of the non-target materials, such as the leaves, are returned to the soil and the solid hurd can be processed further for use in paper, plastics and insulation products. The non-fibrous dust particles created from the decortication of hemp stalks can be compressed into pellets and used as a fuel.
Hemp Fiber Advantages And Benefits
Overall, hemp is arguably superior to other natural fibres, both in terms of cultivation and application. Its many advantages include:
- Fewer inputs required to grow and less water needed than cotton.
- Industrial hemp is pest and disease resistant; partly due to the fact it grows so fast
- Low lignin levels enable environmentally friendly bleaching without the use of chlorine
- Far more fibre can be harvested from hemp than cotton or flax using the same amount of land
- It’s one of the strongest natural fibres
- Less stretch, so clothing retains its shape
- Its softness increases with use
- When dyed, it retains colour better than cotton
- A great insulator
- Anti-bacterial properties
- Excellent breathability
- High abrasion resistance
- Resistant to mold and mildew
- Superior UV blocking attributes
While clothing and other items made from hemp fibre can be a little more expensive in some countries; no doubt pricing will decrease as more of the world again embraces industrial hemp cultivation and processing.
In fact, if it wasn’t for the cotton industry’s influence and the unfair demonising of industrial hemp early last century, many more of us would be wearing hemp clothing and utilising other hemp fabrics today – and the environment would be better off as a result.
No comments:
Post a Comment